What DSPs Do Optics in Space Need?
The space sector is experiencing rapid growth, driven by numerous privately-owned initiatives aiming to reduce the cost of space flight. As this sector expands, it presents new opportunities for developing optical components in space and satellite communications.
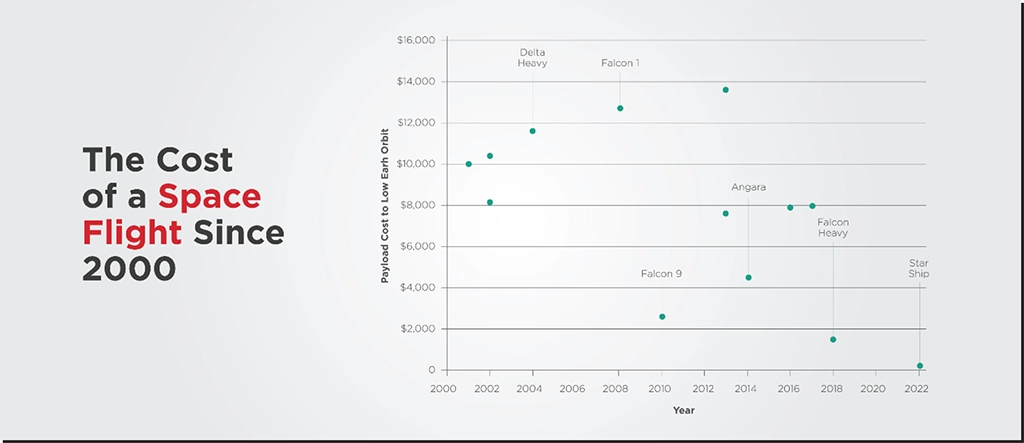
However, the challenges associated with the space environment required digital signal processors (DSPs) optimized for optical communications in space. Unlike traditional fiber transmission systems, DSPs for space need to be optimized for receiver sensitivity and signal-to-noise ratio, adapt to signal recovery in the presence of frequent signal losses, and comply with stringent space certification standards.
Signal to Noise Ratio Over Dispersion
In traditional optical fiber communications, the presence of dispersion often leads to signal distortions that require extensive dispersion compensation techniques. However, space is a vacuum medium devoid of most dispersion-related challenges. Consequently, DSPs developed for space-based optical communications do not require the same level of dispersion compensation as their fiber counterparts. Instead, the primary focus shifts toward optimizing receiver sensitivity and improving the signal-to-noise ratio (SNR) to ensure reliable data transmission in space.
Optical signals travel enormous distances in space and will be extremely weak when they reach a receiver. Focusing DSP performance on enhancing the receiver’s sensitivity enables more accurate detection of these weak optical signals.
To achieve this goal, DSPs for space-based optical communications need forward error correction (FEC) methods that are even more robust than FEC used for ground links. These methods employ sophisticated coding techniques that introduce redundancy in the transmitted data, allowing for efficient error detection and correction.
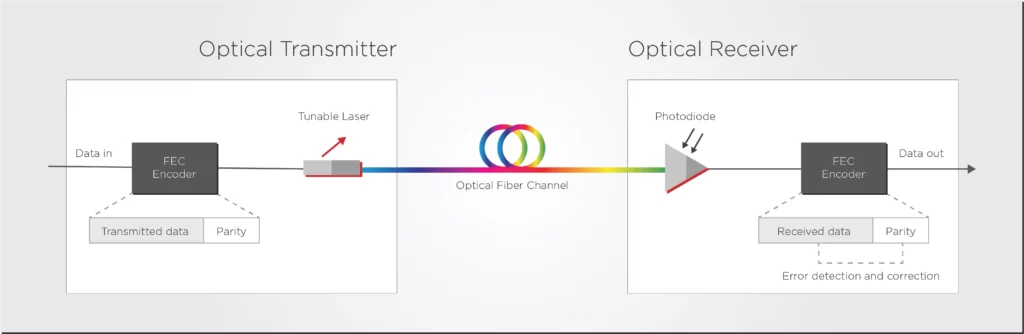
Handling Signal Losses in Space
In contrast to optical fiber communications, where signal losses are typically infrequent but often fatal, space-based optical communications experience more frequent but non-fatal signal losses. Therefore, DSPs designed for space must be optimized to handle these intermittent signal losses and ensure efficient signal recovery.
While DSPs for fiber optical links on the ground often rely solely on their error correction methods, DSPs for space-based optical communications might ask more frequently for the signal to be retransmitted. This retransmission can increase the link latency significantly, which can be compensated in part by using satellite networks to provide more redundancy. You can read more about these satellite networks in one of our previous articles.
Space Certification and Standards
While industrial or commercial temperature certifications are typically sufficient for optical fiber transceivers and their components, DSPs designed for space-based optical communications must adhere to more stringent space certification standards. Space certification ensures that DSPs can withstand the extreme temperatures, vacuum conditions, and radiation exposure prevalent in space environments.
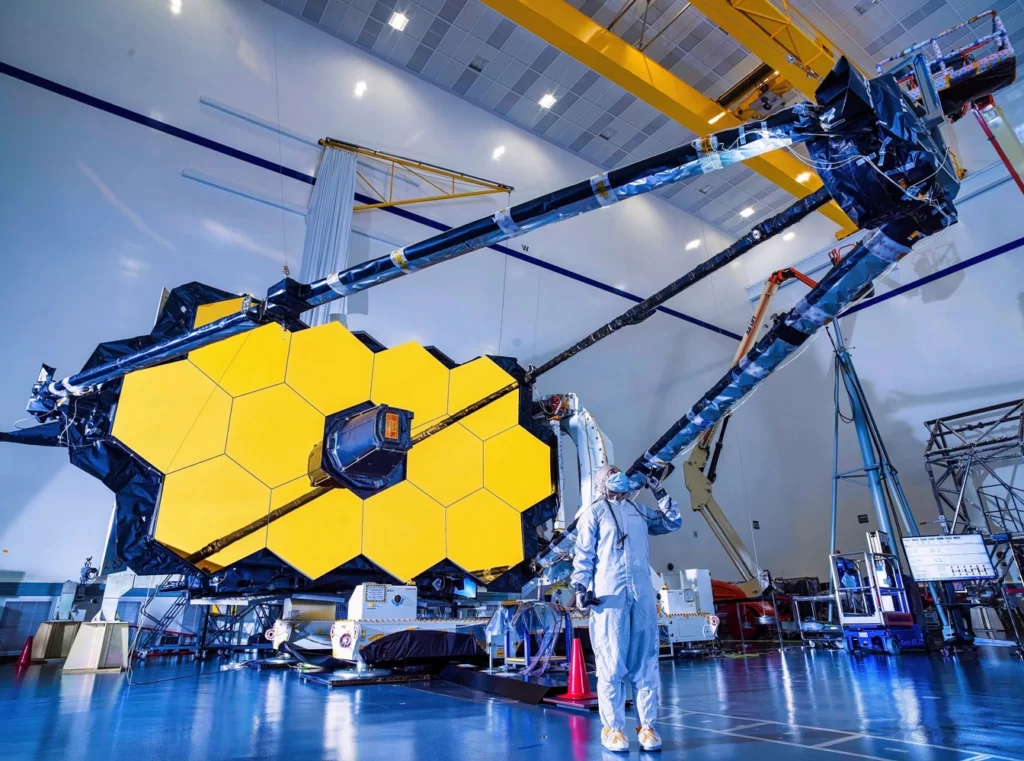
Our testing facilities and partners include capabilities for the temperature cycling and reliability testing needed to match Telcordia standards, such as temperature cycling ovens and chambers with humidity control.
Takeaways
The testing process for photonic integrated circuits ensures their reliability and performance. Device-level testing focuses on individual components, allowing for precise characterization and identification of faulty elements. Functional testing evaluates the overall performance of the PIC, ensuring adherence to design specifications. Reliability testing assesses the robustness and lifespan of the PIC under various operating conditions.